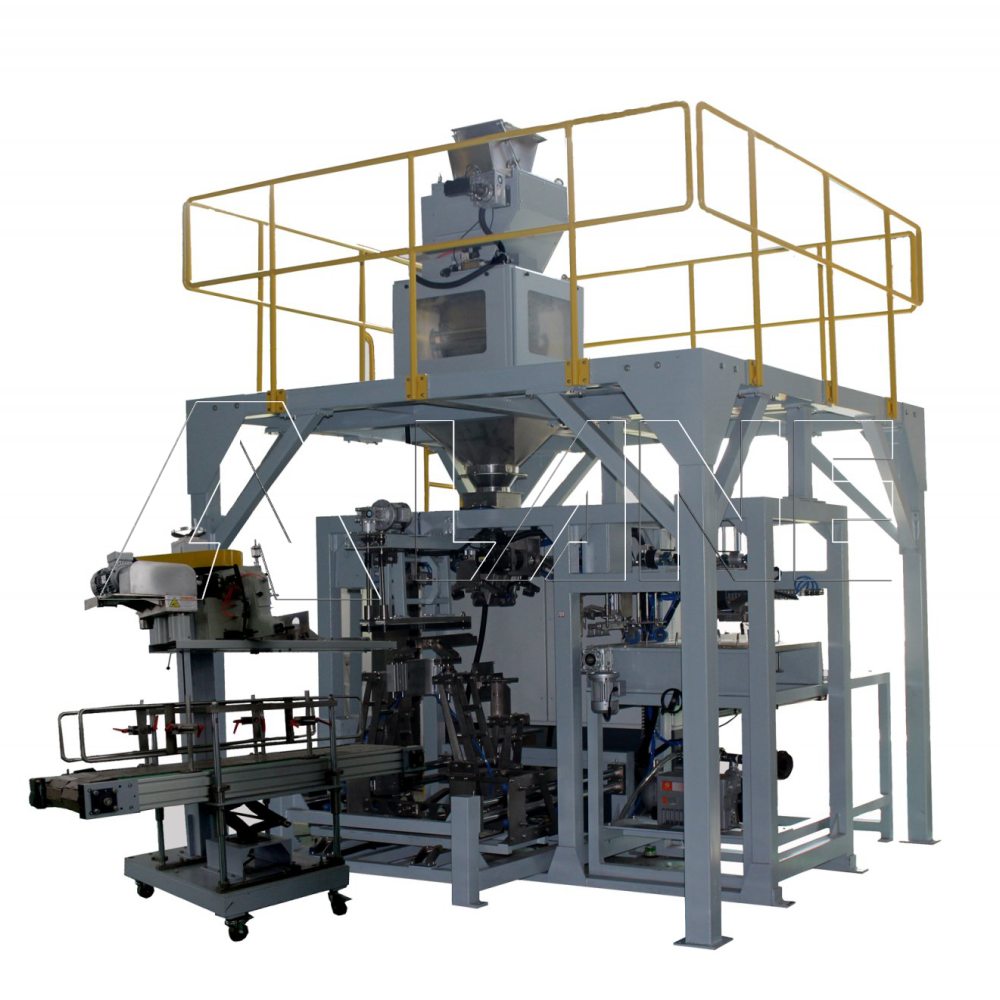
Automatic Packing Machine
The fully automatic packing machine is a packaging equipment that integrates metering, filling and sealing. It adopts advanced automation technology and intelligent control system, which can realize automatic metering, filling, sealing and other operations of materials, greatly improving production efficiency and product quality. Fully automatic packaging machines are widely used in food, medicine, chemical, electronics and other industries, and are suitable for packaging of various powdered, granular and liquid materials. The following is a detailed description of the introduction, composition structure, working process and advantages of the fully automatic packing machine.
Composition Structure
Measuring system: a device for accurately measuring materials. According to the nature of the material and the packaging requirements, different metering methods can be used, such as volumetric metering, weighing metering, etc.
Filling system: a device for filling materials into packaging bags. The filling system usually includes components such as hoppers, conveyor belts, and filling tubes, which can realize fast and accurate filling of materials.
Sealing system: a device for sealing packaging bags. The sealing system usually includes components such as heat sealing knives, cold sealing knives, and ultrasonic sealers, which can achieve sealing and protection of packaging bags.
Control system: a system used to control the operating status and parameters of the fully automatic packaging machine. The control system usually includes PLC controllers, touch screens, sensors and other components, which can realize automatic control and remote monitoring of equipment.
Conveying system: A device used to transport packaged products to a designated location. The conveying system usually includes belt conveyors, roller conveyors and other components, which can realize fast and stable transportation of products.
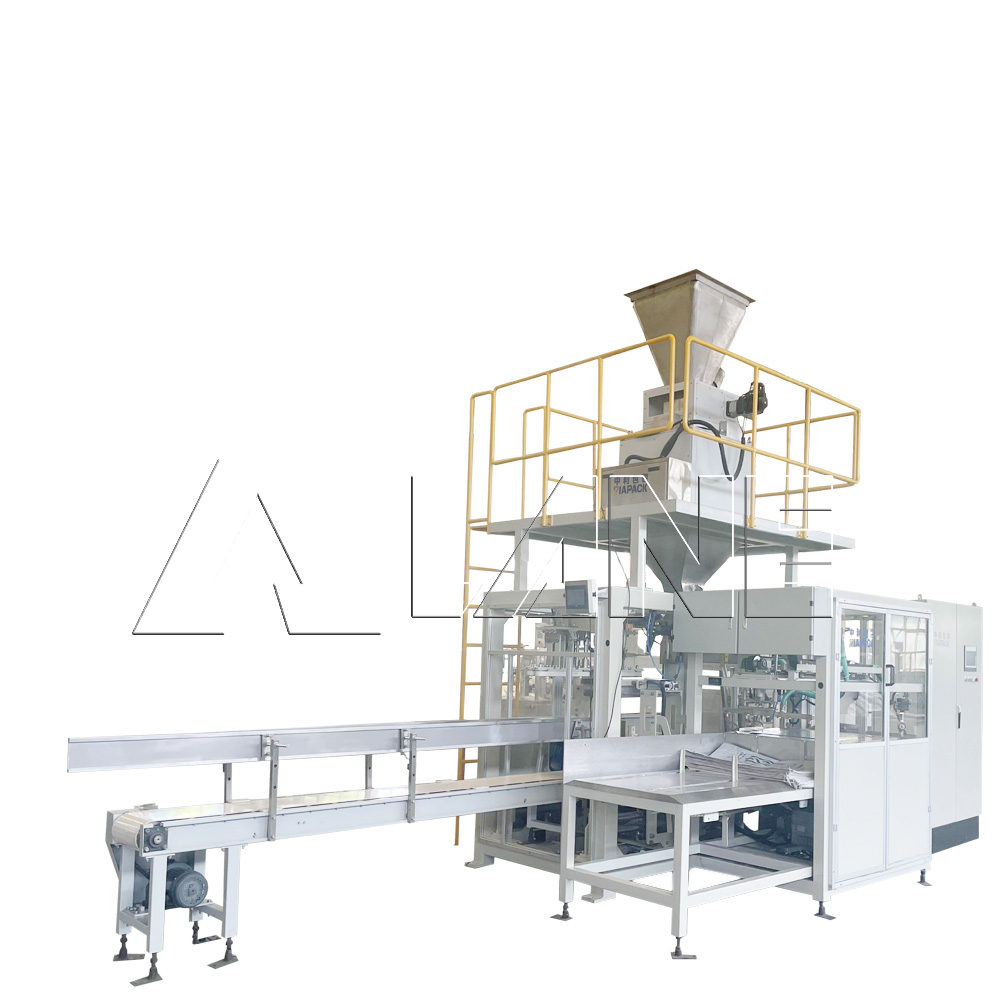
Working Process
Metering: Put the materials to be packaged into the hopper of the fully automatic packing machine, and accurately measure the materials through the metering system. According to the nature of the material and the packaging requirements, different metering methods can be used, such as volumetric metering, weighing metering, etc.
Filling: The measured materials are filled into the packaging bag through the filling system. The filling system usually includes hoppers, conveyor belts, filling tubes and other components, which can realize fast and accurate filling of materials. During the filling process, the filling speed and filling amount can be adjusted as needed to meet the packaging requirements of different products.
Sealing: The filled packaging bag is sealed by the sealing system. The sealing system usually includes heat sealing knives, cold sealing knives, ultrasonic sealers and other components, which can achieve sealing and protection of packaging bags. During the sealing process, the sealing temperature and sealing time can be adjusted as needed to ensure the sealing performance and appearance quality of the packaging bag.
Conveying: The sealed packaging bags are transported to the designated location through the conveying system. The conveying system usually includes components such as belt conveyors and roller conveyors, which can realize fast and stable conveying of products. During the conveying process, the conveying speed and conveying direction can be adjusted as needed to meet the needs of different production lines.
Detection and counting: During the packaging process, the fully automatic packing machine can also detect and count the packaged products through the detection system. The detection system usually includes components such as photoelectric sensors and weight sensors, which can detect parameters such as product size and weight, and classify and count products according to the detection results. At the same time, the detection system can also detect abnormal conditions in the packaging process, such as missing or wrong installation, and issue an alarm or shutdown signal in time to ensure product quality and production safety.
Cleaning and maintenance: After each use, the fully automatic packing machine needs to be cleaned and maintained. When cleaning, turn off the power supply and disconnect the gas source, and then clean and wipe the various components of the equipment according to the requirements of the instructions. During maintenance, check whether the mechanical parts of the equipment are operating normally and whether the electrical parts are safe and reliable. If there are any abnormalities, they should be handled or replaced in time. At the same time, the equipment should be maintained and repaired regularly to extend the service life of the equipment and ensure the normal operation of the equipment.
PACKING RANGE
Advantages
Improve production efficiency: The fully automatic packing machine uses automation technology to realize material metering, filling, sealing and other operations, which greatly improves production efficiency. Compared with traditional manual packaging methods, the fully automatic packaging machine can reduce labor costs and labor intensity and improve production efficiency.
Ensure product quality: The fully automatic packing machine adopts precise metering system and sealing technology to ensure that the material content in each packaging bag is accurate and avoids human errors and pollution. At the same time, the sealing system can ensure the sealing performance and appearance quality of the packaging bag, and improve the market competitiveness of the product.
Wide range of applications: The fully automatic packing machine is suitable for the packaging of various powdered, granular and liquid materials, and is widely used in food, medicine, chemical industry, electronics and other industries. Whether it is solid powder or liquid slurry, the fully automatic packaging machine can provide a suitable packaging solution.
Strong flexibility: The fully automatic packing machine is highly flexible and configurable, and can be adjusted and optimized according to different products and packaging requirements. Users can choose different parameters such as metering methods, filling speed, sealing temperature, etc. according to their needs to meet different production needs.
Easy to operate and maintain: The fully automatic packing machine adopts advanced automation technology and intelligent control system, and the operation is simple and easy to understand. Users can complete the setting and operation of the equipment through the touch screen or buttons. At the same time, the fully automatic packaging machine has a compact structure, is easy to disassemble and clean, and is convenient for users to carry out daily maintenance and maintenance.
Energy saving and environmental protection: The fully automatic packing machine is made of energy-saving design and environmentally friendly materials, which can reduce energy consumption and emissions and meet environmental protection requirements. At the same time, the fully automatic packaging machine can also reduce material waste and environmental pollution and improve resource utilization efficiency.
High safety: The fully automatic packing machine has multiple safety protection measures, such as overload protection, leakage protection, etc., which can ensure the safe operation of the equipment and the safety of the operator. At the same time, the fully automatic packaging machine can also monitor the operating status and parameter changes of the equipment in real time, detect and handle abnormal situations in time, and prevent accidents.
In summary, the fully automatic packing machine has become one of the indispensable important equipment in modern industrial production with its high efficiency, intelligence and flexibility.
Of course, we also offer other types of products for your different needs, you can click to view.
For more information, please contact us by sending an inquiry today! We can help you!