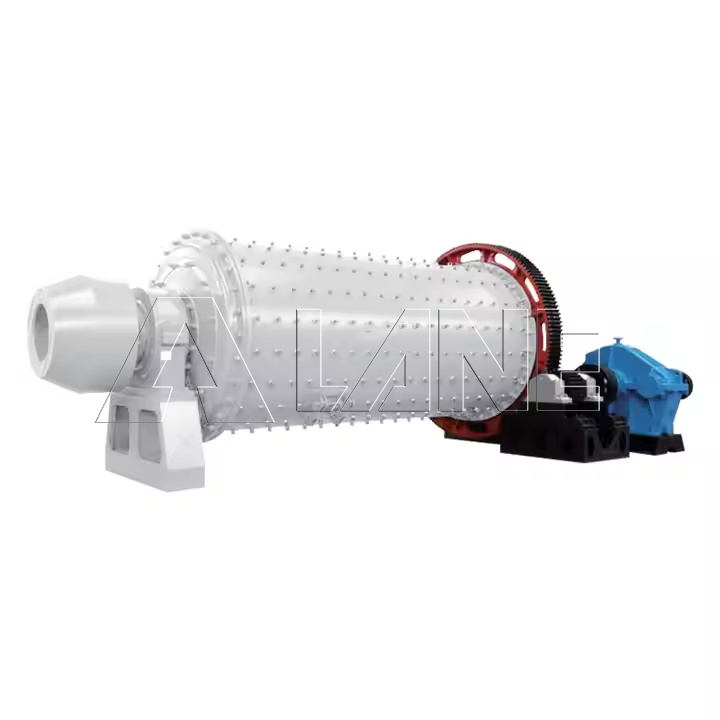
Ball Mill
Ball mill is an important equipment for grinding and crushing materials. It is widely used in powder production lines such as cement, silicate, refractory materials, fertilizers, glass and ceramics, as well as ferrous and non-ferrous metal beneficiation. Ball mill can grind ores and other materials wet or dry, and can handle hard materials such as feldspar, quartz, iron ore, gold ore, etc.
As a widely used mill in beneficiation and cement and ceramic production, it can crush more than 200 kinds of materials, with the characteristics of flexible design, high production capacity, fine particle size, simple structure, low maintenance cost, reliable performance and long service life.
Composition Structure
Cylinder: The core component of the ball mill, usually made of rolled steel plate, with wear-resistant lining on the inner wall. The shape and size of the cylinder vary according to different needs and specifications, but are generally cylindrical or conical. End caps are provided at both ends of the cylinder to close the cylinder and prevent material leakage.
Feeding device: An opening located at the upper part of the cylinder, used to add the material to be ground into the cylinder. The feeding device usually includes a feeding pipe, a feeding hopper and other components, which can control the feeding speed and feeding amount to ensure the stability and continuity of the grinding process.
Discharging device: An opening located at the bottom of the cylinder, used to discharge the ground material. The discharging device usually includes a discharging pipe, a discharging hopper and other components, and the size and shape of the discharging particle size can be adjusted as needed. In order to improve the discharging efficiency and quality, the discharging device can also be equipped with auxiliary equipment such as screens or grate plates.
Transmission system: It includes components such as motors, reducers and belts, which are used to drive the rotation of the cylinder. Whether the design of the transmission system is reasonable or not directly affects the performance and stability of the ball mill. Therefore, when selecting a transmission system, many factors need to be considered, such as motor power, reducer type, belt material, etc.
Lubrication system: It is used to lubricate and cool components such as the transmission system and bearings. The lubrication system can be lubricated by grease or lubricated by thin oil, and the specific choice depends on the use environment and requirements of the equipment. A good lubrication system can reduce the wear and failure rate of the equipment and extend the service life of the equipment.
Control system: used to control the start, stop, feeding, discharging and other operations of the ball mill. The control system can be controlled manually or automatically, and the specific choice depends on the scale and degree of automation of the equipment. Advanced control systems can realize remote monitoring and intelligent management, and improve the operating efficiency and safety of the equipment.
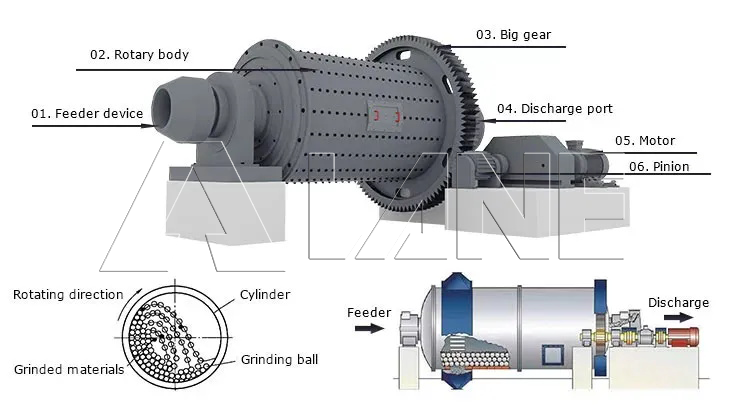
Working Process
Feeding: The material to be ground enters the cylinder through the feeding device. The feeding speed and feeding amount can be controlled by the regulating device to ensure the stability and continuity of the grinding process.
Grinding: The cylinder rotates at a low speed driven by the motor, causing the steel balls or steel forgings to produce impact and friction in the cylinder. Due to the special shape and arrangement of the steel balls or steel forgings, the materials are subjected to multiple impacts and friction during the grinding process, and are gradually ground into the required particle size. At the same time, the materials will collide and rub against each other, further promoting the grinding effect.
Discharging: The ground material is discharged through the discharging device. The size and shape of the discharge particle size can be adjusted by replacing the screen or grate plate of different specifications. According to needs, multiple discharge ports can be set to achieve multi-stage grinding and screening.
Circulation: Some materials that do not meet the requirements can be re-entered into the cylinder through the return device for re-grinding. This ensures that all materials can achieve the expected grinding effect, improves grinding efficiency and product quality.
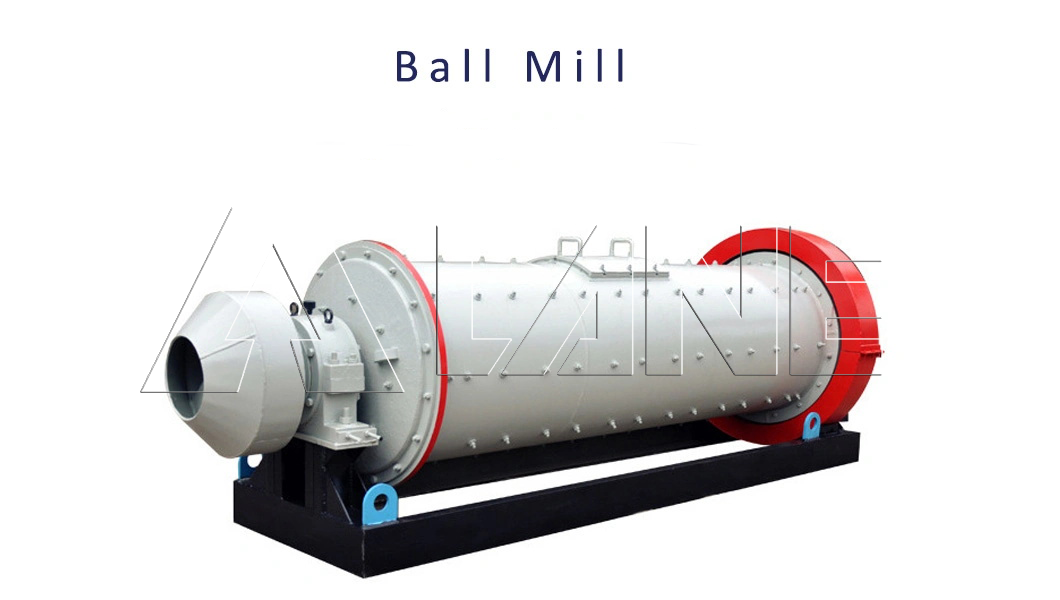
Advantages
High efficiency and energy saving: The ball mill grinds the materials by low-speed rotation, which consumes less energy and is more efficient than other crushing equipment. Under the same energy consumption, the ball mill can process more materials and obtain finer particle size.
Strong adaptability: The ball mill can handle materials of various hardness and humidity, and has strong adaptability. Whether it is brittle or tough materials, whether it is dry or wet materials, the ball mill can effectively perform grinding operations.
Uniform product particle size: Due to the special shape and arrangement of steel balls or steel forgings and the multiple impacts and friction in the cylinder, the particle size of the ground products is uniform and easy to control. This helps to improve the quality and market competitiveness of the products.
Easy maintenance: The structure of the ball mill is relatively simple and easy to maintain. Since the main components such as the cylinder and steel balls or steel forgings are made of wear-resistant materials, the equipment has less wear and a long service life. At the same time, the lubrication and maintenance of the equipment are relatively simple and convenient, which can reduce downtime and maintenance costs.
Excellent environmental performance: During the grinding process, the ball mill produces less dust and lower noise, which meets environmental protection requirements. In addition, the equipment can be equipped with auxiliary equipment such as dust removal devices and sound insulation facilities to further improve environmental performance.
Easy operation: The operation of the ball mill is relatively simple, intuitive and easy to master. Users only need to follow the instructions or operating procedures to complete the grinding operation. At the same time, the equipment is also equipped with a variety of safety protection devices such as overload protection and overheating protection to ensure the safety of operators and the stable operation of the equipment.
Customizable design: According to different needs and material characteristics, the ball mill can be customized to meet specific grinding requirements. For example, the shape and size of the cylinder can be adjusted, the material and size of the steel ball or steel forging can be changed, and the number of discharge ports can be increased or decreased. This flexibility enables the ball mill to better adapt to the needs of different industries and fields.
In summary, the ball mill has become one of the important equipment in the field of powder grinding with its advantages of high efficiency and energy saving, strong adaptability, and uniform product particle size.
Of course, we also offer other types of products for your different needs, you can click to view.
For more information, please contact us by sending an inquiry today! We can help you!